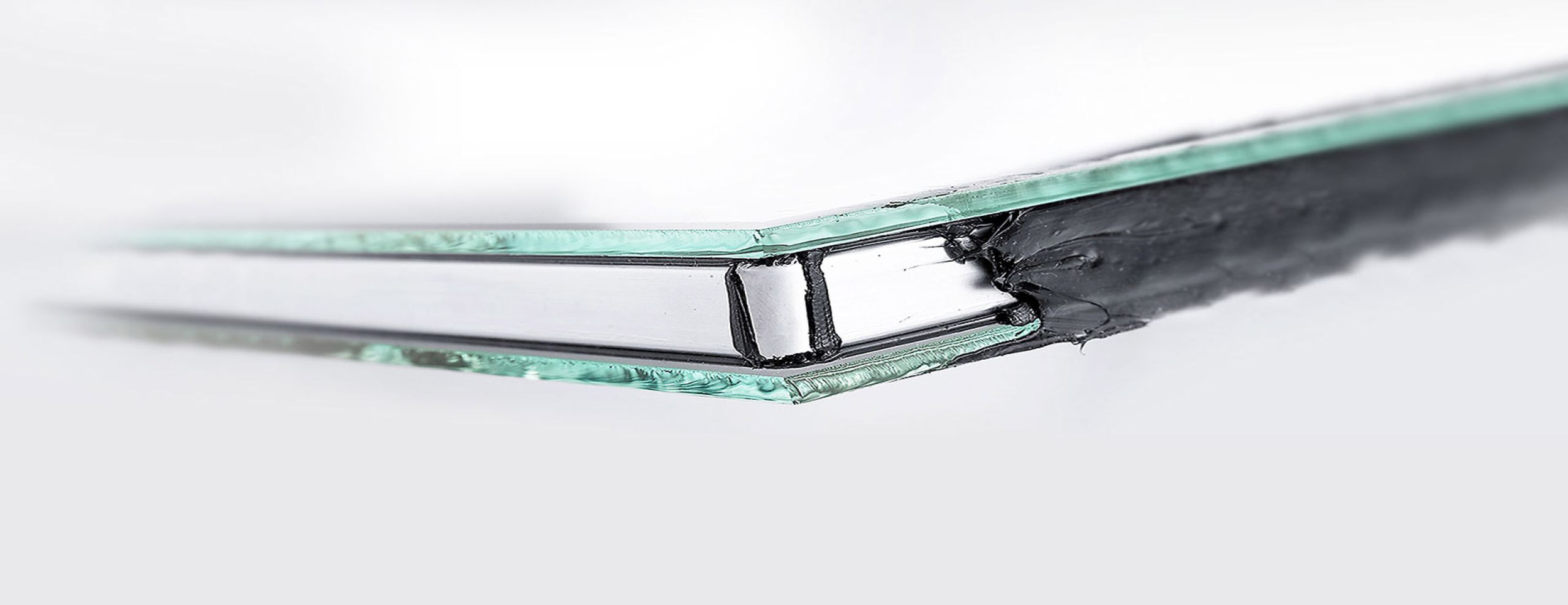
Why self-sealing corner connectors?
Maximum benefit throughout the life cycle
As generally confirmed by experience, the cheapest product is not automatically the cheapest solution. If you expand your decision-making basis by considering the entire life cycle of a solution, it can even happen that the cheapest product leads to the most expensive solution when viewed as a whole.
The right decision always requires a holistic view. In order to follow the path of life cycle-optimized solutions or construction products, the market demands construction products for which not only the theoretical calculated performance is decisive, but also the actual effective performance over the entire life cycle. Effective performance means, on the one hand, taking into account the actual performance deviations of the manufactured construction products as well as the existing performance durability of the construction product throughout its entire life cycle.
In order to achieve the desired technical goals, new approaches are required. Starting with the conventional plastic-only connectors available on the market, the further development of these connectors led to a composition of additional integrated components, each of which further increases the added value of the connector. This multitude of integrated components generates a solution that meets the increased requirements. With the self-sealing corner connectors, a new generation of connecting elements is available for today's market.
In detail, the increase in performance was mainly achieved by optimizing the gas tightness in the corner area. The additional integrated component of a diffusion-tight stainless steel foil and the two integrated butyl strands are responsible for this. In addition, the pull-out forces of the connectors had to be optimized, which is solved by a special wire technology. In addition to the optimized gas tightness, another result is a high level of process reliability, which is reflected in the reduction of the existing performance fluctuations in the insulating glass units produced and thus corresponds to an optimization of the performance stability. The new generation of corner keys thus contributes to the goal of providing life cycle-optimized solutions for today's market.
Optimization of thermal insulation over the service life :
The new self-sealing connecting elements optimize the gas-tightness of the corner area. The open area of a connected frame with corner keys is covered by approximately 90% with a gas-tight stainless steel foil on our innovative corner keys. The remaining area is sealed with the pre-applied butyl. This represents a reproducible solution for frame production in order to achieve optimum process reliability. The area sealed by the stainless steel foil in the corner area can also form a bond with the secondary seal, which in turn increases the gas tightness in the corner area. The more gas-tightness is created, the greater the energy savings throughout the life cycle of the insulating glass.
Reduction of quality fluctuations in insulating glass units produced:
The defined sealing function of the connecting elements achieves a high level of reproducibility and thus eliminates the disadvantages and sources of error associated with error associated with manually sealing the corner with butyle. This minimizes fluctuations in the performance of insulating glass units produced in the corner area. The high retention forces of the wire anchoring solution of the connecting elements also ensures that the sealed corner does not tear open again during the manufacturing process and therefore retains its function. Differing gas contents in the gaps between triple insulating glass panes due to openings in the corners are resolved and excellent gas tightness in the corner area is created over the entire life cycle of the insulating glass. In addition, the problem of possible widening due to bent corners is eliminated and creates a consistent pressed appearance of the insulating glass produced. The gas-tightness performance of the innovative self-sealing corner connectors has already been verified for all three secondary sealants (polysulphide, polyurethane and silicone) in accordance with EN 1279-3.
Aesthetic 90° corner:
The aesthetically perfect corner view enhances the appearance of the visible surface of an insulating glass unit. This plays an increasingly important role, particularly with bonded edge seals and SSG constructions.
Energy saving
With the new innovative products of self-sealing connecting elements, this step is being taken towards life cycle-optimized solutions for the corner areas of an insulating glass unit. The higher the actual performance value and the better the performance durability, the greater the energy-saving effects of the investment.
- Optimization of thermal insulation over the service life
- Reduction of quality fluctuations in insulating glass units producedan
- aesthetic 90° corner in the insulating glass unit for an outstanding appearance