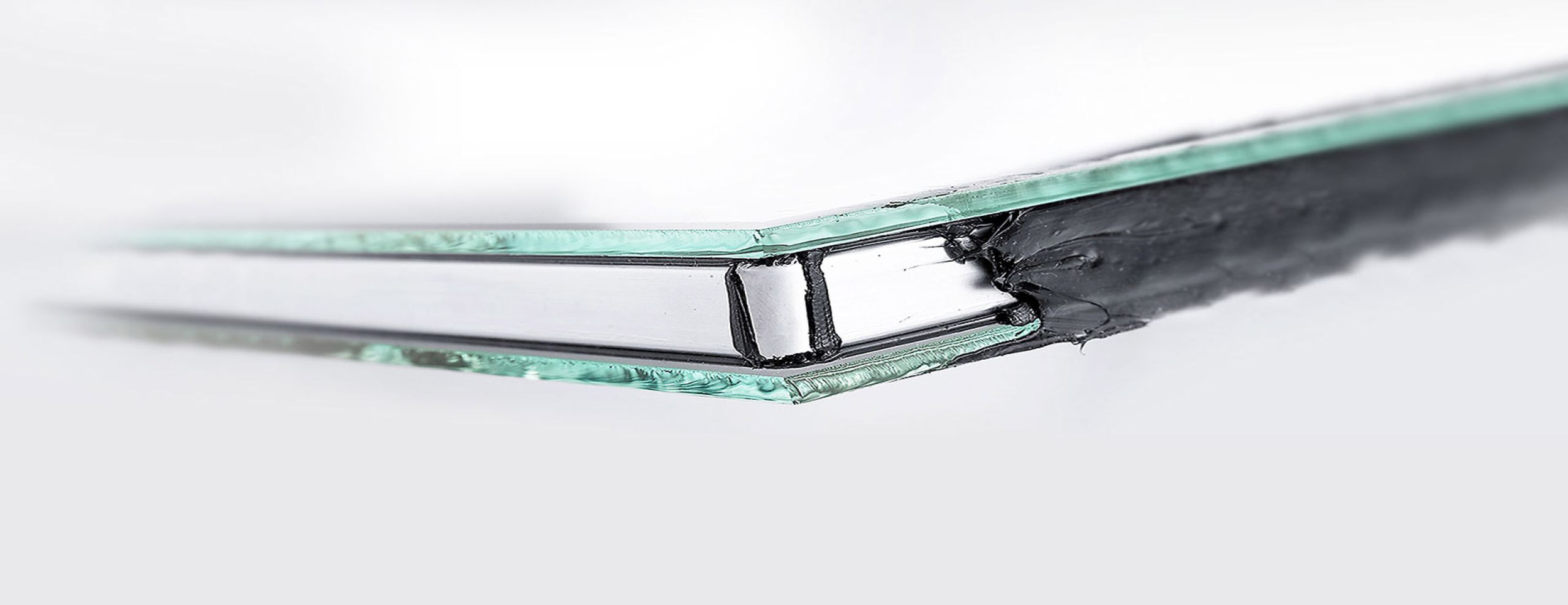
Maximum process reliability
Reduction of quality fluctuations
The defined sealing function of the connecting elements achieves a high level of reproducibility and thus eliminates the overall disadvantages and sources of error caused by manually sealing the corner with butyle. This minimizes fluctuations in the performance of insulating glass units produced in the corner area. The high retention forces of the wire anchoring solution of the connecting elements also ensure that the sealed corner does not tear open again during the manufacturing process and therefore retains its function. Differing gas contents in the gaps between triple insulating glass panes due to openings in the corners are resolved and excellent gas tightness in the corner area is created over the entire life cycle of the insulating glass. In addition, the problem of possible widening due to bent corners is eliminated and creates a consistent pressed appearance of the insulating glass produced. The gas-tightness performance of the innovative self-sealing corner connectors has already been verified for all three secondary sealants (polysulphide, polyurethane and silicone) in accordance with EN 1279-3.
Fast processing thanks to integrated sealing
No investment in machinery is required for frame production. There is no need for time-consuming conversion of bending machines to the respective spacer, minimizing the overall time required for conversion to different profile types and thus creating greater flexibility in production. For processing, only the transparent protective film needs to be torn off in one go and can then be inserted into the spacer.
High gas tightness over the service life for optimized effective Ug values
The self-sealing connecting elements optimize the gas tightness of the corner area. Approximately 90% of the area in the corners of the frame is covered by these corner keys with a gas-tight stainless steel foil. The remaining area is sealed with the pre-applied butyl. These integrated components achieve a reproducible solution for frame production in order to create optimum process reliability. The area sealed by the stainless steel foil in the corner area can also form a bond with the secondary seal, which in turn increases the gas tightness in the corner area. The more gas-tightness is created, the greater the energy savings throughout the life cycle of the insulating glass.
Aesthetic 90° corner
The aesthetically perfect corner view enhances the appearance of the visible surface of an insulating glass unit. This plays an increasingly important role, particularly with bonded edge seals and SSG constructions.
All corner connectors are available in the different profile colors of the spacers.
Reasons for a change
The switch to self-sealing connecting elements brings numerous advantages and meets today's growing demands on insulating glass production.
- Maximum process reliability to reduce quality fluctuationsfast
- processing thanks to an integrated seal
- high gas tightness over the service life for optimized effective Ug values
- aesthetic 90° corner for the visual appearance