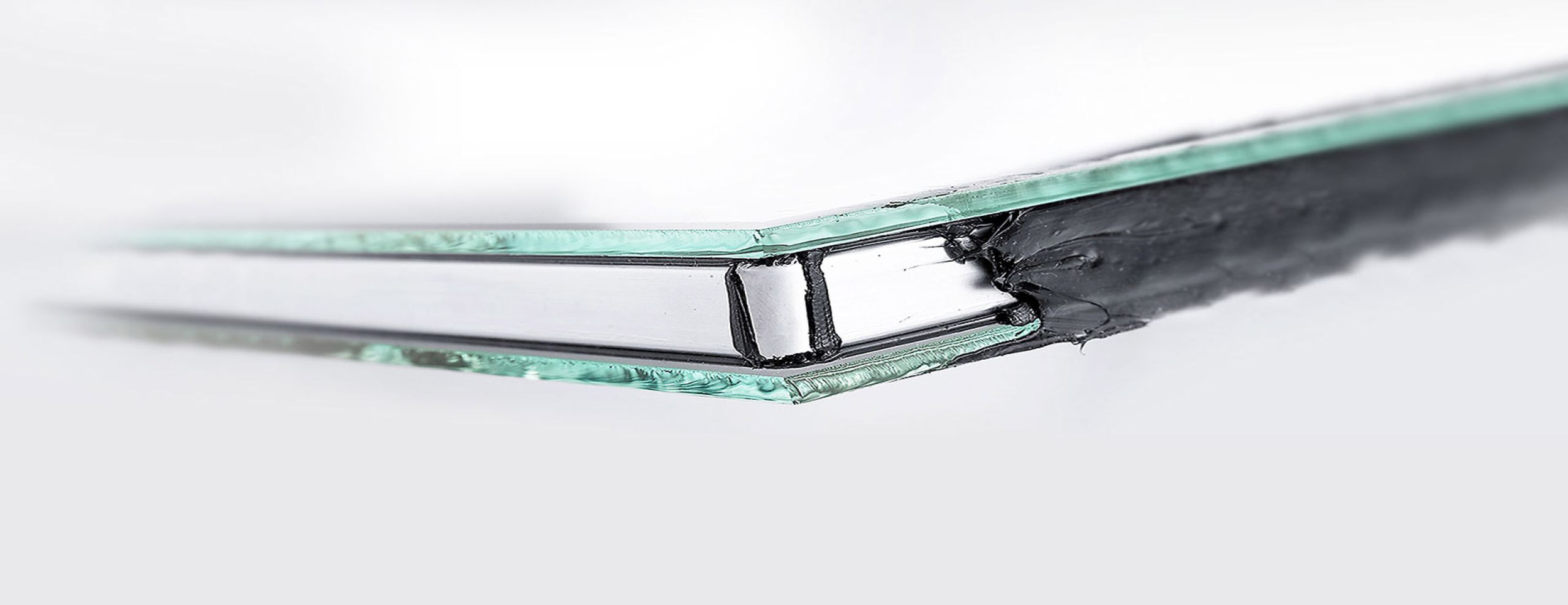
Self-sealing corner keys
The intelligent solution for insulating glass and for its production
Increasing market requirements and the goal of staying ahead of the market are driving the continuous further development of construction products and their preliminary products. The shift from product optimization up to the day of sale to product optimization based on consideration of the entire life cycle is affecting more and more areas of various industries. In order to meet these increasing requirements in the area of insulating glass units, the innovative self-sealing corner connectors now offer the possibility of opting for a life cycle-optimized product solution.
The self-sealing corner connectors generate added value by maximizing the performance of insulating glass throughout its life cycle and by reducing fluctuations in the quality and performance of the insulating glass manufactured within a production run.
INTEGRATED COMPONENTS
Based on the conventional plastic-only connectors available on the market, their further development has led to a composition of additional integrated components, which ultimately increases the added value of the connector. This multitude of integrated components generates a solution that meets the increased requirements. With the self-sealing corner connectors, a new generation of connecting elements is available for today's market.
OPTIMIZATION OF GAS TIGHTNESS
A central element of the new self-sealing connecting elements is the optimization of gas tightness in the corner area of an insulating glass unit. During production, the corner area is one of the most critical areas of the product. The problem with assembling a frame with corner connectors is that an open area is created in the corner of the frame which means that the diffusion barrier is interrupted. As a solution, the self-sealing corner connector has an integrated gas-tight stainless steel foil, which restores the diffusion barrier over almost the entire interrupted area. The remaining open area is sealed with the pre-applied butyl strip. This defined sealing function of the connecting elements achieves a high level of reproducibility for the first time and eliminates the disadvantages and sources of error associated with manual butyling of the corner. This process-safe, defined sealing of the corner not only prevents gas loss during the assembly of an insulating glass unit, but also increases the gas tightness of the insulating glass to reduce gas losses during the life cycle as much as possible in order to maintain the maximum thermal insulation value of the insulating glass throughout its life cycle.
The self-sealing corner connector not only optimizes the primary seal, but also offers advantages with regard to the secondary seal. The aforementioned stainless steel foil also has the property that this metallic surface in the corner area can also form a connection with the secondary seal, which in turn increases the gas tightness in the corner area. The more gas-tightness is created, the greater the energy-saving effect of the insulating glass throughout its life cycle.
WIRE ANCHORING SOLUTION
Another positive factor is the unique wire anchoring solution. The resulting high pull-out forces ensure that the sealed corner does not tear open again during the manufacturing process and therefore retains its function. This additional increase in process reliability ultimately optimizes reproducibility and guarantees performance consistency. In other words, the high reproducibility also results in a minimization of the differences in quality and performance of the insulating glass in production, which leads to lower tolerances of the specified Ug-value with regard to thermal insulation.